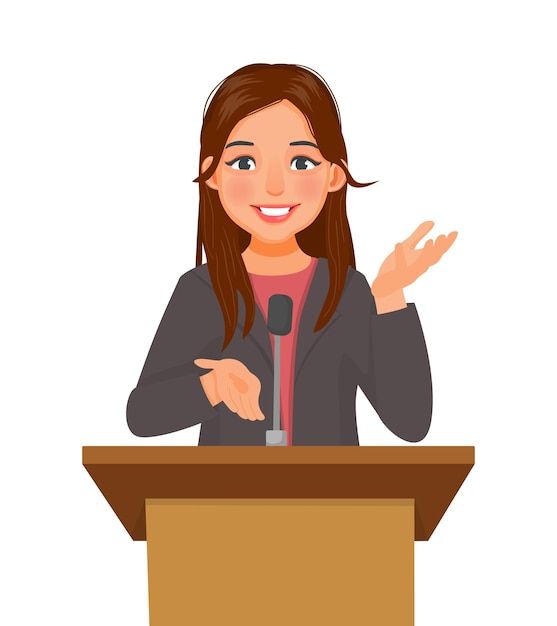
Piping Engineering Services
Our piping team delivers efficient, innovative designs by combining expertise in materials,
stress analysis, and corrosion resistance for industrial and oil and gas projects.
Our piping team delivers efficient, innovative designs by combining expertise in materials,
stress analysis, and corrosion resistance for industrial and oil and gas projects.
We specialize in developing and stamping both new and existing line class specifications, ensuring accuracy and adherence to industry standards.
An engineer is shown performing stress calculations for a 3D engineering model in a modern workspace, surrounded by technical documents and tools.
We specialize in defining piping and equipment metallurgies tailored to project requirements and operational environments. Our expertise ensures optimal material selection for durability, safety, and performance.
Experienced piping engineering services include system design, material selection, stress analysis, and 3D modeling. These services ensure safe, efficient, and compliant piping installations. Professionals also provide inspection, maintenance, and troubleshooting for existing systems. Expertise in project management and regulatory compliance is essential for success.
Developing and stamping new and existing line class specifications involves creating detailed guidelines for materials, pressure, temperature, and flow within piping systems. It ensures compliance with industry standards and project requirements. The process includes thorough review, validation, and approval of these specifications for accuracy and safety. This work is crucial for maintaining system integrity and optimizing performance in both new and existing installations.
Preparing stress calculations for the engineering model involves analyzing forces such as internal pressure, thermal expansion, and external loads. It ensures the piping system can withstand operational conditions without failure. The process includes selecting materials with sufficient strength to handle calculated stresses.Compliance with industry standards is essential for safe and reliable system design.
Defining piping and equipment metallurgies involves selecting materials based on their mechanical properties, corrosion resistance, and compatibility with operational conditions. It ensures that the materials can withstand temperature, pressure, and chemical exposure. Proper metallurgy selection prevents system failures and extends service life. Compliance with industry codes and standards is critical for safety and reliability.
Piping line class specifications define the detailed requirements for the materials, design, and construction of piping systems within an industrial project. These specifications outline the types of pipes, fittings, valves, and flanges to be used, based on factors like pressure, temperature, and fluid type. They ensure that the piping system can withstand operational conditions and meet safety standards. Line class specifications are essential for uniformity, quality control, and compliance with industry codes. Properly defined line classes improve system reliability, reduce risks, and ensure cost-effective operation.
Co-stamping line lists with process engineering involves collaboration between piping and process engineering teams to finalize and validate the materials and specifications for each piping line. The process ensures that the piping system design aligns with the process flow and operational requirements. Co-stamping ensures that both mechanical and process aspects are considered, maintaining system safety and efficiency. It helps to resolve any discrepancies between design and process conditions, ensuring compliance with standards. This joint effort enhances project accuracy, reduces errors, and optimizes system performance.
Construction Work Packages (CWPs) are detailed documents that outline the scope, materials, resources, and schedule for a specific construction task or portion of a project. These packages ensure that work is completed in an organized and efficient manner, with clear instructions for each phase of construction. Requests for Information (RFIs) are formal queries raised during construction to clarify project details or resolve uncertainties in design, specifications, or scope. RFIs help address potential issues promptly, preventing delays or errors. Both CWPs and RFIs are essential for maintaining project timelines, quality, and compliance with design specifications.
Piping specialty item lists and datasheets provide detailed specifications for unique or non-standard components in a piping system, such as valves, expansion joints, and special fittings. These documents outline material requirements, dimensions, pressure ratings, and other critical attributes. They ensure that specialized components meet design, safety, and operational requirements. Properly maintained lists and datasheets help streamline procurement, manufacturing, and installation processes.
Valve lists and datasheets provide essential information about the types, sizes, materials, and specifications of valves used in piping systems. They include details such as pressure ratings, temperature limits, and operation types, ensuring the valves meet system requirements. These documents support procurement, installation, and maintenance processes by ensuring proper selection and functionality.
Tie-in lists and isometric materials are critical for integrating new piping systems with existing infrastructure. Tie-in lists detail the connection points, pipe sizes, and locations where new pipes will be joined to existing systems. Isometric materials provide visual representations and detailed dimensions of these connections, helping to plan and execute the installation accurately.
Material Take-Offs (MTOs) are detailed lists that identify and quantify all materials required for a project, based on design drawings and specifications. MTOs help in cost estimation, procurement, and inventory management by providing a clear breakdown of materials such as pipes, fittings, and valves. Request for Quotation (RFQ) documents are issued to suppliers to obtain pricing and delivery terms for the materials listed in the MTO
Commodity purchase specifications for pipe and fittings outline the detailed requirements for materials, dimensions, pressure ratings, and testing standards. These specifications ensure that the purchased components meet the necessary industry codes, such as ASTM, ASME, or ANSI, and are suitable for the intended operating conditions. They typically include information on material types (e.g., carbon steel, stainless steel), coating requirements, and any special manufacturing or inspection processes.
P&ID valve and specialty item tagging involves assigning unique identifiers or tags to valves, fittings, and other specialized components on Process and Instrumentation Diagrams (P&IDs). These tags help clearly identify each item, making it easier to locate, reference, and maintain throughout the lifecycle of the system. The tagging system typically follows standardized naming conventions to ensure consistency and clarity across engineering documents.
Technical bid evaluations involve assessing and comparing the technical aspects of bids submitted by suppliers or contractors in response to a project’s requirements. This process ensures that the proposed solutions meet the project's specifications, quality standards, and technical criteria. Evaluations focus on factors like compliance with design standards, material specifications, technical approach, and timeline. A thorough technical evaluation helps identify the most suitable vendor or contractor while mitigating risks and ensuring project success.