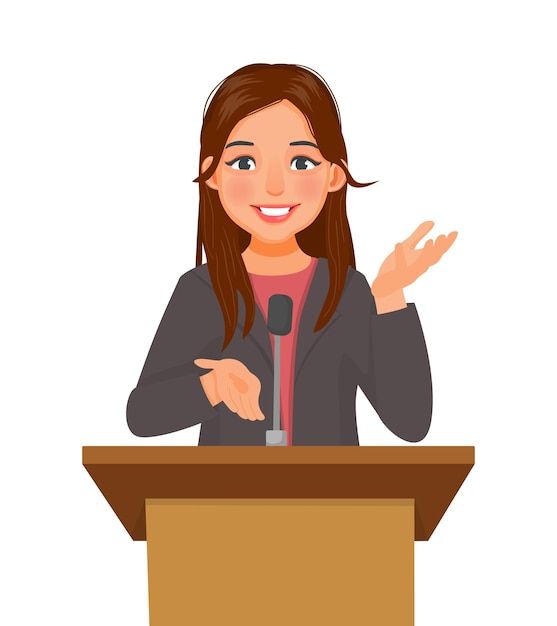
Process Engineering Consulting Services
We excel in crafting and optimizing vital processes that drive efficiency and innovation in complex engineering projects.
We excel in crafting and optimizing vital processes that drive efficiency and innovation in complex engineering projects.
We specialize in designing and developing critical processes for complex projects, ensuring every workflow is optimized with precision and efficiency.
We specialize in creating and refining process simulations for complex projects, ensuring every scenario is modeled with accuracy and precision.
We specialize in analyzing and enhancing processes for complex projects, ensuring every operation is optimized for maximum efficiency and precision.
EmirCorp Projects has been a trailblazer in the field of process engineering, delivering innovative and high-quality solutions. By harnessing our extensive expertise and cutting-edge technology, our process engineering services have been pivotal in streamlining operations and driving the success of projects across the globe.
Process design is the systematic planning and development of workflows, procedures, and systems to achieve specific objectives in production or operations. It involves defining the sequence of steps, resources, and conditions required to transform inputs into desired outputs efficiently. This process ensures optimal performance, safety, and cost-effectiveness while meeting quality standards. It often utilizes tools like flowcharts, simulations, and software to visualize and refine processes.
Process simulation is the use of computer models to replicate and analyze real-world processes in a virtual environment. It allows engineers to study the behavior of a system under various conditions without disrupting actual operations. By simulating workflows, materials, and resource interactions, it helps identify inefficiencies, predict outcomes, and test improvements. This approach reduces risks, saves costs, and enhances decision-making by providing insights before implementing changes. Process simulation is widely used in industries like manufacturing, chemical engineering, and supply chain management to optimize performance and achieve desired outcomes.
Process optimization is the practice of improving processes to increase efficiency, reduce costs, and enhance performance. It involves analyzing existing workflows, identifying bottlenecks, and implementing changes to streamline operations. This can include adjustments in resources, equipment, or technology to achieve better outcomes with minimal waste. Process optimization focuses on maximizing productivity while maintaining or improving quality and safety standards. It is an ongoing effort that uses data-driven insights and continuous improvement strategies to ensure optimal performance over time.
Material and energy balance is a fundamental concept in process engineering, used to ensure that resources are efficiently utilized in a system. It involves accounting for all the inputs, outputs, and accumulations of materials and energy within a process. Material balance ensures that the amount of raw material entering a system equals the amount of material leaving the system, taking into account any accumulation within the system. It is used to track and optimize the use of materials, reduce waste, and improve efficiency. Energy balance involves accounting for all the energy entering, leaving, and being stored in a system.
Process safety refers to the management of potential hazards associated with industrial processes to prevent accidents, injuries, and environmental damage. It involves identifying, assessing, and mitigating risks throughout the design, operation, and maintenance of processes. The goal is to ensure the safe handling of materials, proper functioning of equipment, and adherence to safety protocols to prevent catastrophic failures. Key components of process safety include hazard analysis, safety instrumented systems, risk assessments, and emergency response planning. It also emphasizes the importance of training, safety audits, and continuous monitoring to maintain a safe working environment.
Cost estimation is the process of forecasting the financial resources required to complete a project, task, or operation. It involves calculating direct and indirect costs associated with labor, materials, equipment, overhead, and other factors. Accurate cost estimation is crucial for budgeting, resource allocation, and ensuring profitability while avoiding cost overruns. There are different methods for cost estimation, including analogous estimation (based on historical data from similar projects), parametric estimation (using mathematical models and data to predict costs), and bottom-up estimation (summing up individual cost elements).
Equipment satisfaction refers to the level of performance, reliability, and overall effectiveness of equipment in meeting the needs and expectations of its users or operators. It encompasses factors such as the equipment's efficiency, durability, ease of use, and its ability to complete tasks within the desired time frame. In industrial and engineering contexts, equipment satisfaction can be assessed through feedback from operators, maintenance teams, and performance metrics like uptime, downtime, and repair frequency. High equipment satisfaction indicates that the equipment is reliable, cost-effective, and contributes positively to operational productivity. Conversely, low satisfaction might suggest that the equipment requires upgrades, replacement, or changes in how it is used or maintained.
Control strategy design is the process of developing a plan for managing and regulating the behavior of a system or process to achieve desired outputs while maintaining efficiency, safety, and stability. It involves selecting and implementing control methods that govern how variables such as temperature, pressure, flow rates, or chemical concentrations are maintained within a set range. In industrial and process engineering, control strategies can be based on different control methods, including feedback control (where the system adjusts based on output deviations), feedforward control (anticipating disturbances and adjusting inputs proactively), and advanced control techniques (like model predictive control or adaptive control).
Quality control QC in process engineering refers to the systematic activities and procedures used to ensure that products, services, or processes meet predefined quality standards and specifications. It involves monitoring and testing materials, components, or processes to detect and correct defects or variations. QC methods typically include statistical analysis, sampling techniques, and inspections to verify that processes are consistent and outputs are within acceptable tolerances. The goal is to prevent defects, reduce waste, and maintain high standards of quality throughout production. In industries like manufacturing, chemical processing, and pharmaceuticals, quality control ensures product reliability, safety, and compliance with regulations.
Troubleshooting is the methodical process of identifying and resolving issues within a system or operation. It involves diagnosing problems such as equipment failure, process inefficiencies, or deviations from expected performance. Engineers analyze data, such as sensor readings and process parameters, to detect the root cause of the problem. Corrective actions, such as adjusting controls, repairing equipment, or modifying procedures, are then implemented to restore normal operations.
Seize the opportunity to enhance your operational productivity with EmirCorp Projects. Our experts thoroughly analyze your current processes, identifying bottlenecks and inefficiencies, and then deliver tailor-made solutions engineered to streamline operations, reduce waste, and cut costs. Making process efficiency not just an objective, but an achievable reality.
Leverage the power of innovation with EmirCorp Projects. Our team stays abreast of the latest technologies in process engineering. We help integrate these advancements seamlessly into your operations, enhancing efficiency and giving your business the competitive edge, it requires in today’s dynamic industrial landscape.
Our team at EmirCorp Projects specializes in meticulously identifying and addressing the root cause of process failures. By conducting thorough investigations and utilizing advanced analytical tools, we provide actionable insights that help avoid future issues and maximize operational efficiency.
EmirCorp Projects ensures that your process operations adhere to all industry standards and legal regulations. With our deep understanding of statutory requirements, we help maintain compliance, avoiding potential fines and ensuring uninterrupted business operations.
Safety is a priority for every industry. At EmirCorp Projects, we excel in identifying potential process-related hazards and providing solutions to mitigate these risks. Our systematic approach ensures a safer workspace, shielding your employees, equipment, and the environment.
Trust EmirCorp Projects to conduct comprehensive feasibility studies for your new projects or modifications to existing ones. We assess technical, economic, and logistical aspects, ensuring the viability of your initiatives and paving the way for successful endeavors.
At EmirCorp Projects, we design new processes and redesign existing ones to improve efficiency or meet new requirements. We utilize our extensive experience along with modern design approaches to provide solutions that bring tangible improvements to your operations.
Process simulation is a vital element of our service repertoire at EmirCorp Projects. We make use of cutting-edge software tools to model and predict the behavior of your process operations under various conditions, allowing for effective troubleshooting and optimization.
At EmirCorp Projects, we prioritize verifying that your processes operate as per their design and intentions. Through our rigorous process validation, we ensure consistency, reliability, and alignment with your business goals, enhancing your overall operational efficiency.
EmirCorp Projects is committed to assisting you in driving the quality of your end product or service. By identifying and addressing issues in the process, we help improve overall quality, resulting in enhanced customer satisfaction and business growth.
Leave the management of your process engineering projects to us. At EmirCorp Projects, we oversee every aspect from inception to completion, ensuring projects are delivered on time, within budget, and to your exacting standards, facilitating a hassle-free project experience for you.
Maximize your operational economy with EmirCorp Projects. We take an in-depth look at your process engineering systems and find smart, sustainable ways to reduce operational and maintenance costs. Our cost-optimization strategies are designed to deliver significant cost benefits over the entire lifecycle of the process.
Redefine your supply chain efficiency with EmirCorp Projects. We assess and optimize the processes involved in your supply chain, improving logistics, reducing costs, and enhancing overall efficiency. Our adept consultation can be the catalyst for a more streamlined and cost-effective supply chain, bolstering your bottom line.
Choosing the right equipment is pivotal in process engineering. EmirCorp Projects assists in the identification, selection, and procurement of the appropriate equipment and technologies for your process. Our expertise ensures optimal performance and compatibility with your operational requirements.